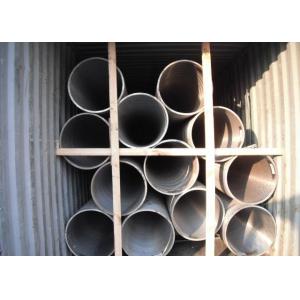
Add to Cart
Industrial Seamless Alloy Steel Pipe , Seamless Steel Tube ASTM A335 Standard
Specialized in providing various steel pipes for more than 10 years, TIPTOP offers ASTM A335 seamless large caliber & heavy wall thickness pipe with competitive price, premium quality and flexible delivery time. Third party inspection is available.
TIPTOP offers a comprehensive range of ASTM A335/ASME SA335 P12 high pressure steel pipe for the right technical solution, with wall thickness from Sch 10 to 140mm & OD up to 56’’.
1. Available Size Range
OD | Thickness | ||
mm | inch | mm | SCH |
88.9~1422 | 3''~ 56'' | 2.11~140 | ≥SCH10 |
*If the steel grades and size you are looking for are not listed above, please contact us for further information. |
2. Standards:
ASTM A335 Standard Specification for Seamless Ferritic Alloy-Steel Pipe for High-Temperature Service
3. Application:
For the low and medium pressure boiler and steam header pipes;
For the high-pressure boiler and steam pipes, and the petrochemical industry pipes;
Power plant; Chemical Fertilizer; Petrochemicals; Offshore Oils; Gas Productions; Refineries and etc.
4. Ordering Information
Quantity (feet, meters, or number of lengths),
Name of material (seamless alloy steel pipe),
Grade (P12),
Manufacture (hot-finished or cold-drawn),
Size using one of the following:
NPS and schedule number;
Outside diameter and nominal wall thickness;
Outsider diameter and minimum wall thickness;
Inside diameter and nominal wall thickness;
Inside Diameter and minimum wall thickness.
Length (specific or random)
End finish (plain end or bevel end)
5. Chemical Requirements
Chemical Requirements | |||||||||
Grade | UNS Designation | Composition, % | |||||||
C | Mn | P max | S max | Si | Cr | Mo | Others | ||
P12 | K11562 | 0.05-0.15 | 0.30-0.61 | 0.025 | 0.025 | 0.50 max | 0.80-1.25 | 0.44-0.65 | ... |
6. Tensile Requirements
Tensile Strength min.: 60ksi / 415MPa
Yield Strength min.: 32ks / 220MPa
7. Inspection & Test
Chemical composition, mechanical properties ( tensile strength, yield strength, elongation, flaring, flattening, bending, hardness, impact test), surface and dimension, NDE, hydrostatic test.
8. Manufacture
Hot Rolled or Cold Drawn
9. Manufacturing Process
Raw Material Inspection → Cold Centering → Heating → Piercing & Rolling → SIzing → Heat Treatment → Testing → Finishing → NDE → Visual & Dimension Inspection → Marking → Storing & Shipping
10. Supplementary Requirements
S1. Product Analysis
S2. Transverse Tension Tests
S3. Flattening Test
S4. Metal Structure and Etching Tests
S5. Photomicrographs
S6. Photomicrographs for Individual Pieces